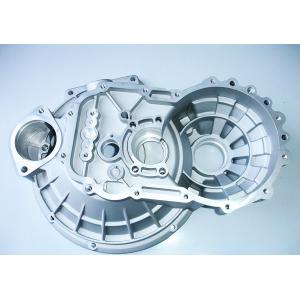
Add to Cart
Precision casting process aluminum products precision casting parts Lightweight and Strong Precision Casting for High-Performance Aluminum Products
Aluminum Casting
Aluminum casting is the process of producing aluminum products by melting aluminum and its alloys, pouring it into molds, and allowing it to cool and solidify. Aluminum casting is widely used in various industries, including automotive, aerospace, and machinery, due to its lightweight, high strength, corrosion resistance, and good machinability.
Melting: The first step in aluminum casting is to heat aluminum and its alloys to their melting point (approximately 660°C) until they become liquid. This process can be carried out in arc furnaces, resistance furnaces, or induction furnaces.
Pouring: The molten aluminum is then poured into pre-made molds, which are typically sand molds or metal molds. Pouring can be done through gravity casting or pressure casting, depending on the desired characteristics of the cast part and production scale.
Cooling and Solidification: As the molten aluminum cools and solidifies in the mold, it takes the shape of the mold. Controlling the cooling process is critical for the final product's quality. Rapid cooling can lead to cracks within the casting, while slow cooling may cause deformation.
Post-processing: After casting, aluminum products may require post-processing, such as sandblasting, machining, heat treatment, and surface finishing to enhance their performance and appearance.
Inspection: Finally, aluminum products undergo a series of quality inspections to ensure they meet design standards and requirements.
Due to its unique advantages, aluminum casting is increasingly becoming an indispensable part of modern manufacturing.